In a competitive market, customer focus is the key to success. The ambition of ArcelorMittal Belgium is to grow into the preferred supplier of our customers in terms of service and quality. For that reason, it is important to have uniform and sustainable systems and processes for order processing, planning, follow-up, transport and quality of the finished products.
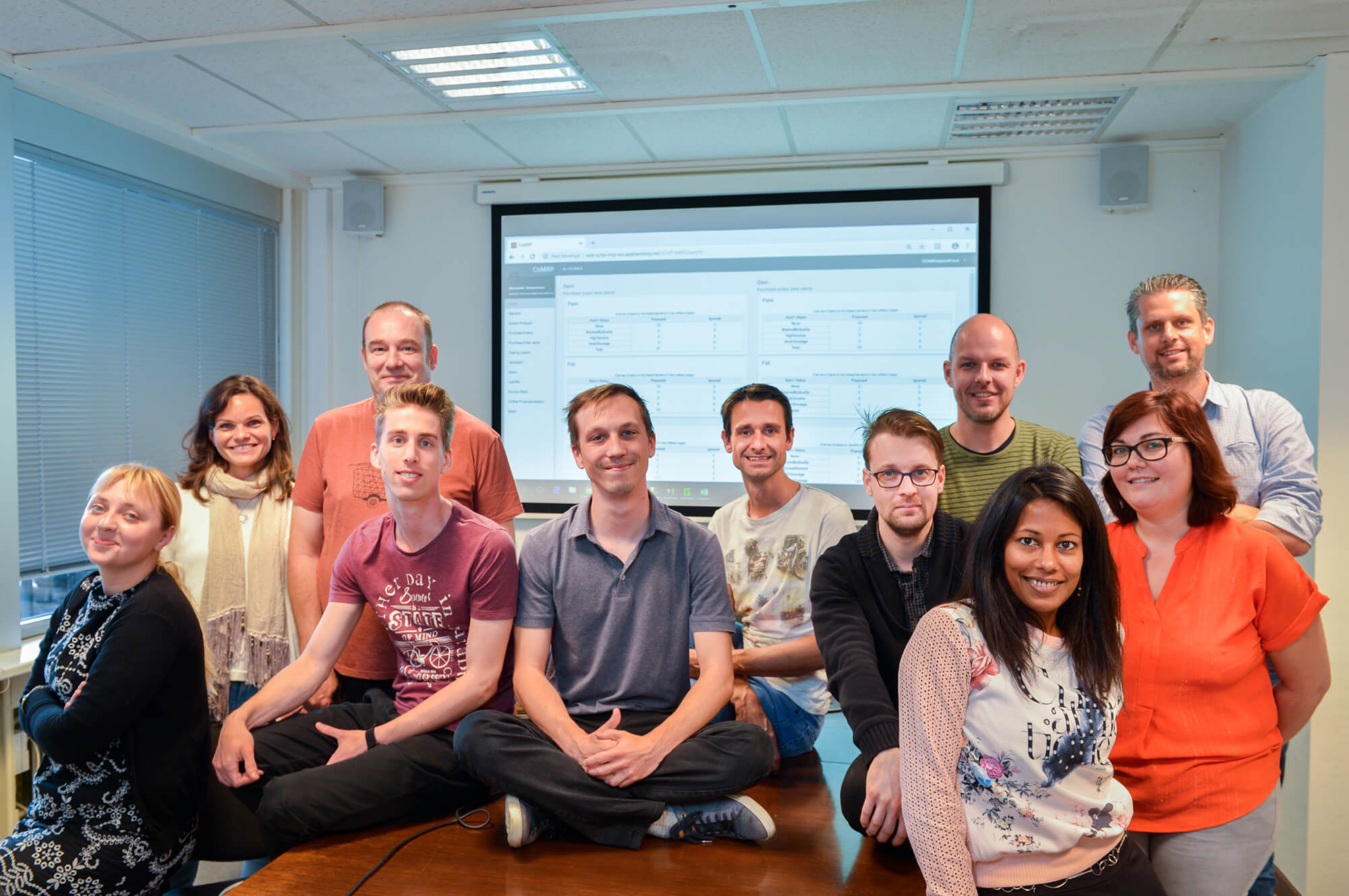
Scale-up (Supply Chain, Quality Chain, European Project)
The Scale-up (Supply Chain, Quality Chain, European Project) project of ArcelorMittal Europe - Flat Products drives the strategic processes in terms of ‘supply chain’ and quality. Our cluster is a pilot for two part-projects of Scale-up:
One Order book
By 2020, we will evolve towards one common order book. It means that the Liège lines will be considered as an extension to the Ghent lines and no longer as two separate entities. Thanks to One Order book, it will be possible to move material from Ghent to Liège and vice versa if this is necessary for the service to our customers. Naturally, it will require us to switch to uniform systems in Ghent and Liège, which will be interlinked.
Quality tracking
We are building one collective system to monitor quality. In this context, we apply bar codes to finished coils, before sending them to our customers. This confirms our leading role in innovation.
Groundbreaking all weather terminal in the port of Ghent
ArcelorMittal Gent, the Flemish investment company PMV, Euroports and North Sea Port are collaborating on achieving the very first covered loading dock and warehouse in Ghent: the All Weather Terminal or AWT. The new terminal will be build next to our existing general cargo dock and will primarily be used for the storage and shipping of our finished coils. In addition, 20% of the storage capacity can be used for trading other materials and mixed cargo.
With the new AWT, we want to further boost our services to our customers. Loading high-grade steel used to be only possible in dry weather, whereas – thanks to the AWT- it will now be possible 24/7, independent of the weather conditions. The AWT is also an investment in sustainability, since the greater shipping capacity per vessel also saves a considerable volume of freight transport (up to 25,000 lorries per year). ArcelorMittal Belgium wants to develop into a frontrunner in terms of sustainable logistics.
The contract was signed mid-June 2018, the construction started in May 2019. It is anticipated that the All Weather Terminal will be operational by autumn 2020.
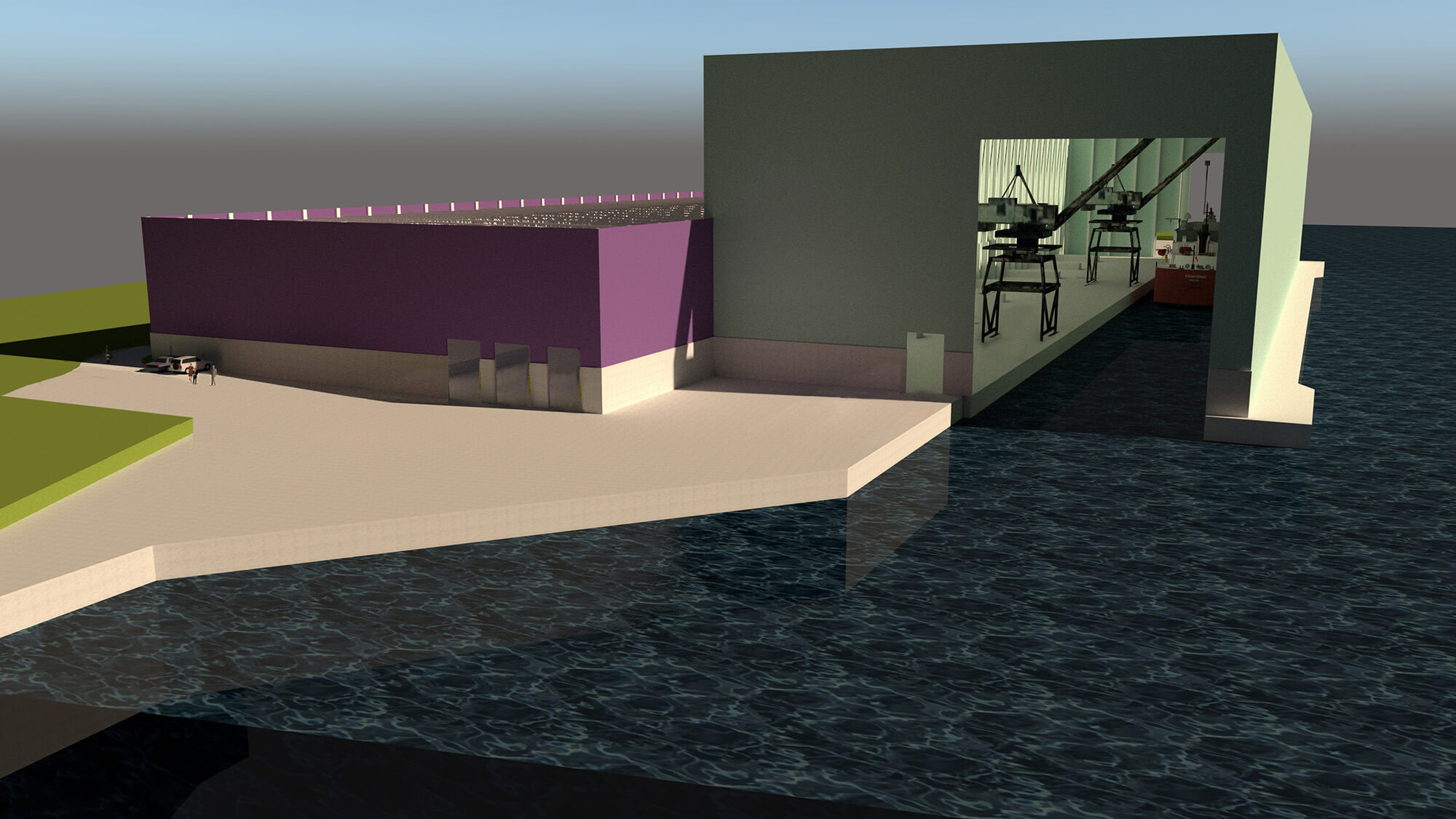
25,000trucks less/year
New track & trace app
Together with a few logistics partners, our company has developed a system for real time tracking and tracing. All parties involved can use the app to track consignments at every step of the way, from the planning stage until the delivery to the customer.
We deliver over six million tons of steel per year to hundreds of destinations inside and outside of Belgium and Europe. Every day, up to five hundred lorries, one hundred train wagons and several inland waterways vessels and seagoing vessels leave our sites. From now on, these goods can be followed - with the help of the track & trace app - from the point of departure from our company to their end destination.
The application is already used by our customers, as well as by our commercial organisations. Thanks to the Scale-up project, data of many other sites are also available, which means that the app can be used by many other customers aside from those of the Ghent and Liège sites. An extension has also been arranged, making it possible to monitor every urgent consignment.
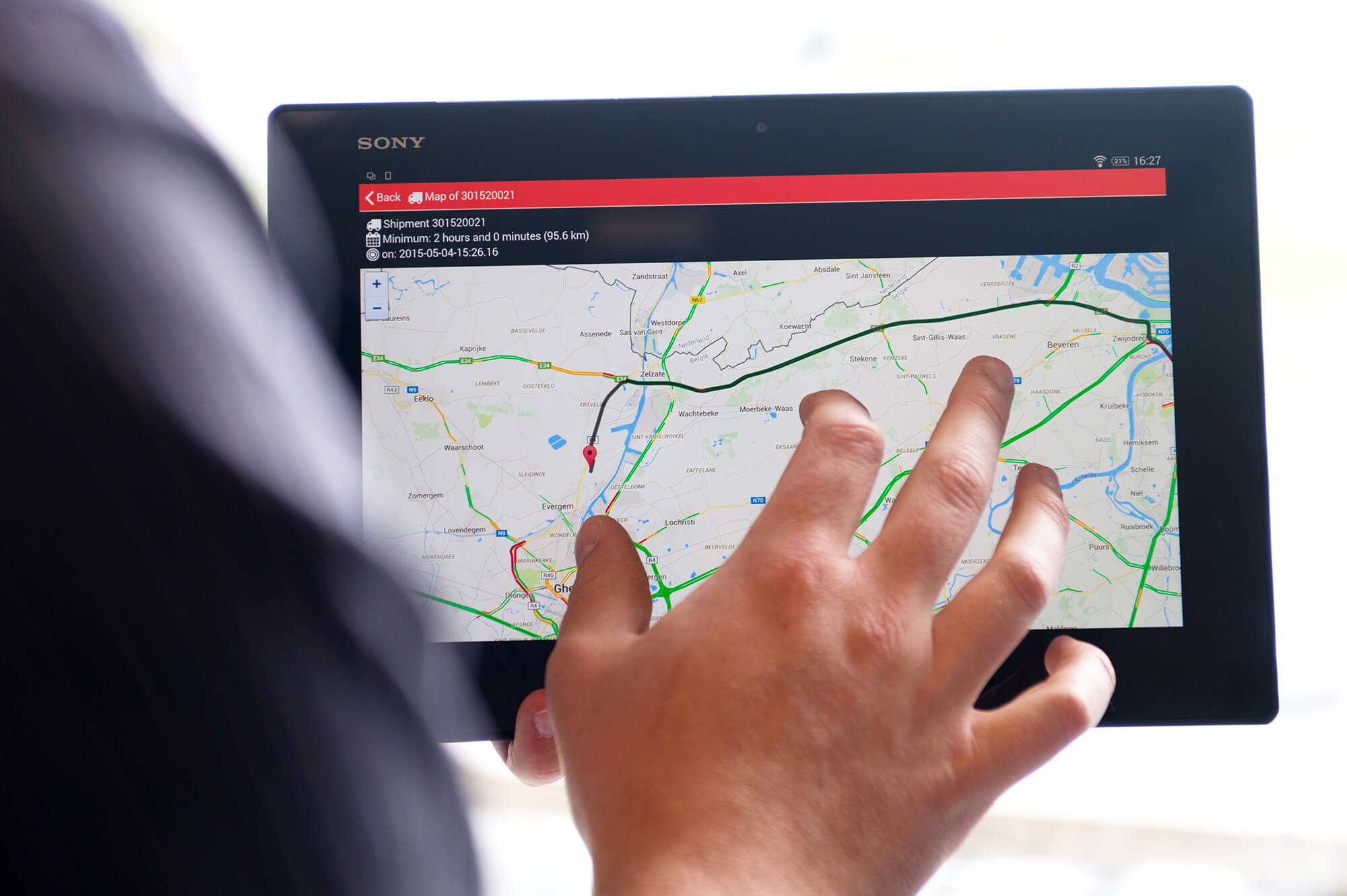
ArcelorMittal Belgium breaks production records
Cost price leadership is an absolute must for attracting orders and investments. It has become clear that we achieve a good cost position when our production volume is high. In 2018, ArcelorMittal Belgium set no less than seven production records.
The WCM culture of continuous improvement and the focus on increasing operational reliability of our installations naturally contributed to the achievement of this result. However, this success is first and foremost thanks to the dedication and the excellent teamwork performed by all collaborators of the sections and departments involved. It confirms that that the contribution of every one counts and matters.
No less than seven production records:
1,391 KT
Pickling line - Tandem mill n° 2 Ghent
270 KT
of which 165 kt organically
coated Combiline Liège
476 KT
Continuous annealing line Liège
516 KT
Eurogal Liège
265 KT
Temper rolling mill n° 3 Ghent
5,553 KT
Hot strip mill Ghent
2,259 KT
Tandem mill TTS Ghent
Customer Day 2018 with inauguration of SIDGAL 3 upgrade
On 8 November 2018, we held a Customer Day to formally introduce a new ultra-modern furnace in our hot dip galvanising line to over 150 European industrial and automotive customers. At the same time, we also officially inaugurated the new furnace in the presence of Honorary Governor Jan Briers. The furnace makes it possible to achieve highly sophisticated and very specific temperature curves. With it we are now able to galvanise our high strength steels which are up to 20% lighter whilst simultaneously being very strong and readily transformable. This investment forms the final element of the Fortiform® investment chain. The customer day included an academic session, product conferences and a guided tour through the brand-new production line.