04 Une utilisation efficace des ressources naturelles et un taux de recyclage élevé
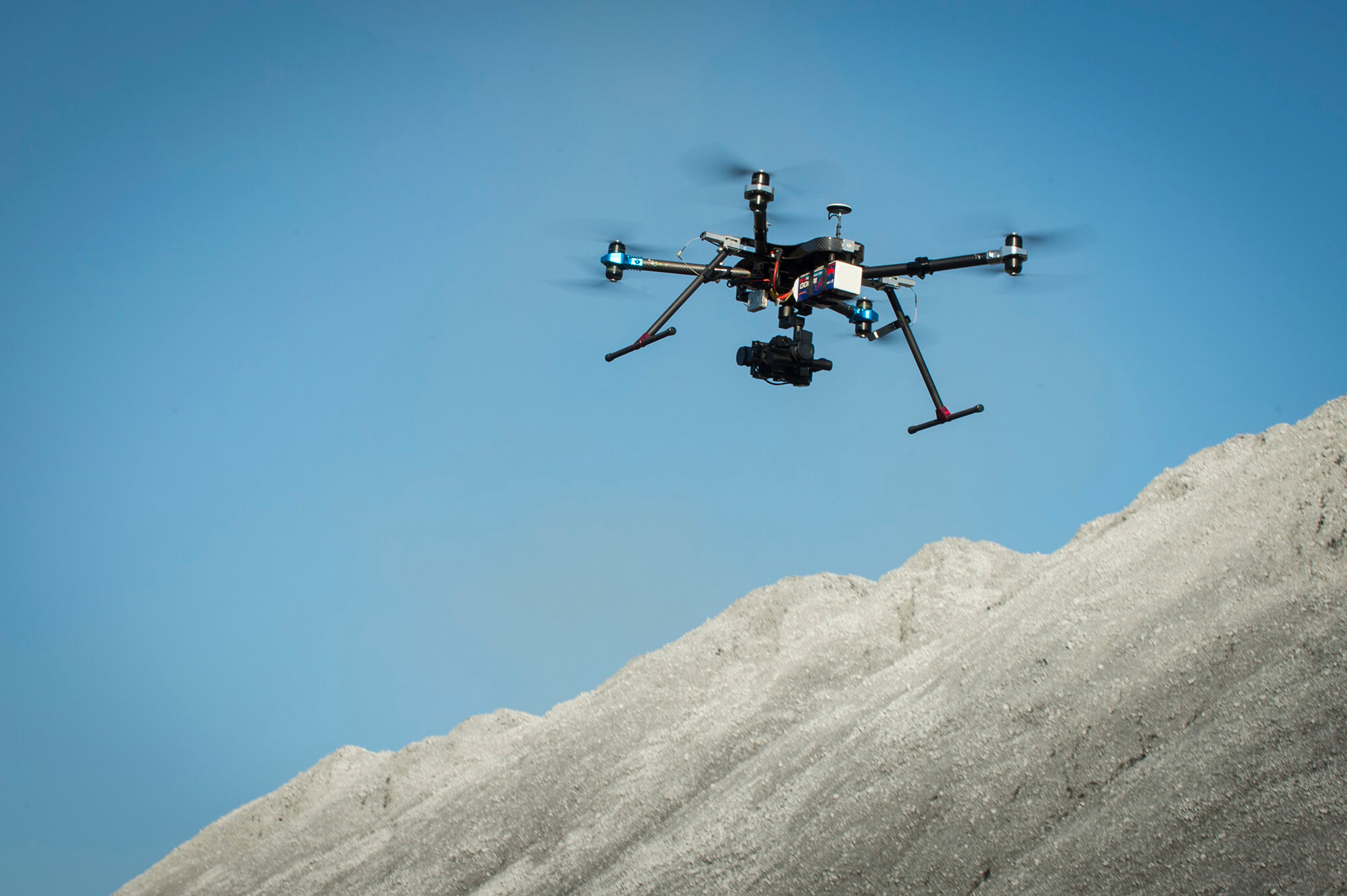
Notre contribution à la protection de l'environnement
Notre contribution à la protection de l'environnement
« Nous continuons à afficher des progrès en matière de gestion environnementale à tous les niveaux de l'organisation. »
Depuis 2001, nous nous sommes dotés d’un système de gestion environnementale conforme aux critères fixés par la norme internationale ISO 14001. Ce système de management environnemental nous oblige à attaquer notre gestion environnementale de façon structurée, en commençant par l'identification des aspects environnementaux importants auxquels nous devons prêter attention. Chaque année, le système de management environnemental est soumis à un audit par une organisation externe indépendante qui détermine si nous continuons à respecter toutes les normes et à améliorer notre gestion environnementale. Le certificat ISO 14001 garantit à tous les intéressés externes, tels les riverains, les entreprises environnantes, les gouvernements, les fournisseurs et les clients, que quand nous disons vouloir être une « entreprise durable », ce ne sont pas des paroles en l'air.
Le premier certificat ISO 14001 commun pour le cluster ArcelorMittal Belgium
11/‘18
audit de suivi ISO 14001 chez ArcelorMittal Gand
12/‘18
audit de certification et d'extension ISO 14001 chez ArcelorMittal Liège
01/‘19
le nouveau certificat ISO 14001 a officiellement été attribué à l'ensemble du cluster ArcelorMittal Belgium
Le 18 mars 2019
Des amines divisent le CO et le CO2 pour traitement ultérieur
Le 18 mars 2019, ArcelorMittal Gand et Dow (Terneuzen) ont annoncé de travailler avec plusieurs partenaires à une technologie innovante pour valoriser chimiquement (à l'aide d'amines) le CO et le CO2 des gaz de l'industrie sidérurgique, un projet intitulé « Carbon2Value ». L'installation pilote a été livrée sur notre site gantois en 2018. Après inspection et après une phase d'essai approfondie, nous avons pu démarrer le programme de tests au printemps 2019. L'inauguration officielle de l'installation pilote a eu lieu le 18 mars 2019 en présence du Ministre flamand de l'Emploi, de l'Économie, de l'Innovation et du Sport, Philippe Muyters.
« Notre projet Carbon2Value est un bel exemple d'une symbiose industrielle entre deux industries diverses, l'industrie sidérurgique et l'industrie chimique, pour réduire les émissions de CO2. »
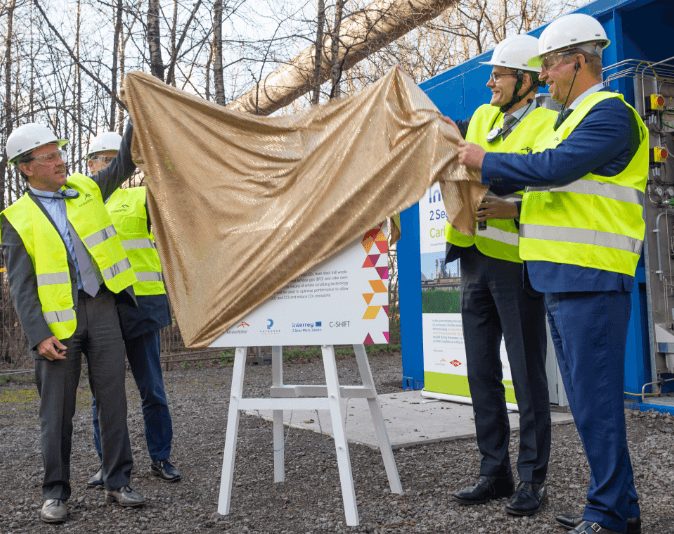
Le 2 mai 2019
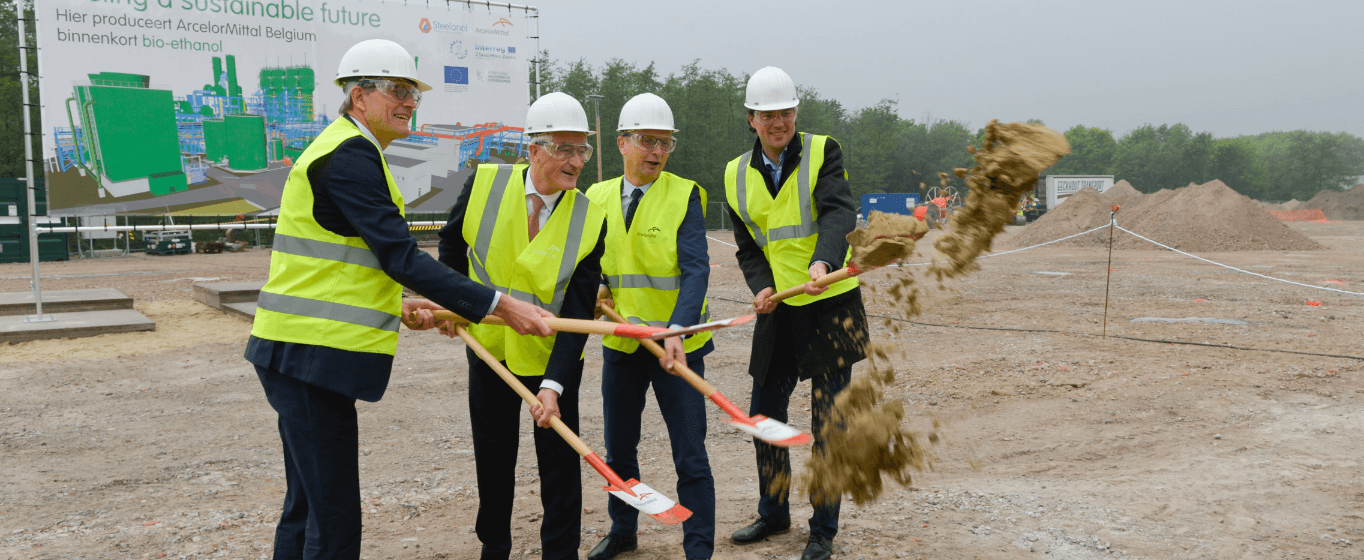
Le jeudi 2 mai 2019, le premier coup de pioche a été donné en présence du Ministre-Président flamand Geert Bourgeois dans le cadre de la construction de deux nouvelles installations révolutionnaires destinées à réduire encore davantage les émissions de carbone d'ArcelorMittal Gand.
Le gaz de haut fourneau transformé en bioéthanol
Nous pourrons transformer une partie du CO que nous séparons par notre installation pilote Carbon2Value en bioéthanol par le biais de l'installation Steelanol pour l'utiliser ensuite comme combustible de transport ou pour la production de matériaux synthétiques.
« Notre installation Steelanol sera la première installation industrielle européenne de son genre, avec une production annuelle de 80 millions de litres de bioéthanol. »
Cette technologie, sous licence de la société américaine LanzaTech, avec qui nous avons conclu un partenariat, utilise des microbes qui se nourrissent de monoxyde de carbone pour produire du bioéthanol. La mise en service et la première production de l'installation Steelanol sont prévues pour 2020.
Transformation de déchets de bois en biocharbon
L'installation Torero transformera les déchets de bois en biocharbon adapté au procédé des hauts fourneaux. Cela nous permettra de diminuer l'injection dans nos hauts fourneaux de charbon pulvérisé fossile, de réduire ainsi nos émissions de CO2 et d'apporter une alternative à l'incinération actuelle de ce flux de déchets de bois particulièrement difficile.
« Dans une première phase, l'installation Torero transformera 120 000 tonnes de déchets de bois en près de 50 000 tonnes de biocharbon par an. »
La technologie de ce processus de torréfaction a été développée par la société Torr-Coal. Les déchets de bois seront fournis par Renewi. La mise en service et la première production sont prévues pour fin 2020.