04 Efficiënt gebruik van natuurlijke rijkdommen en een hoge recyclagegraad
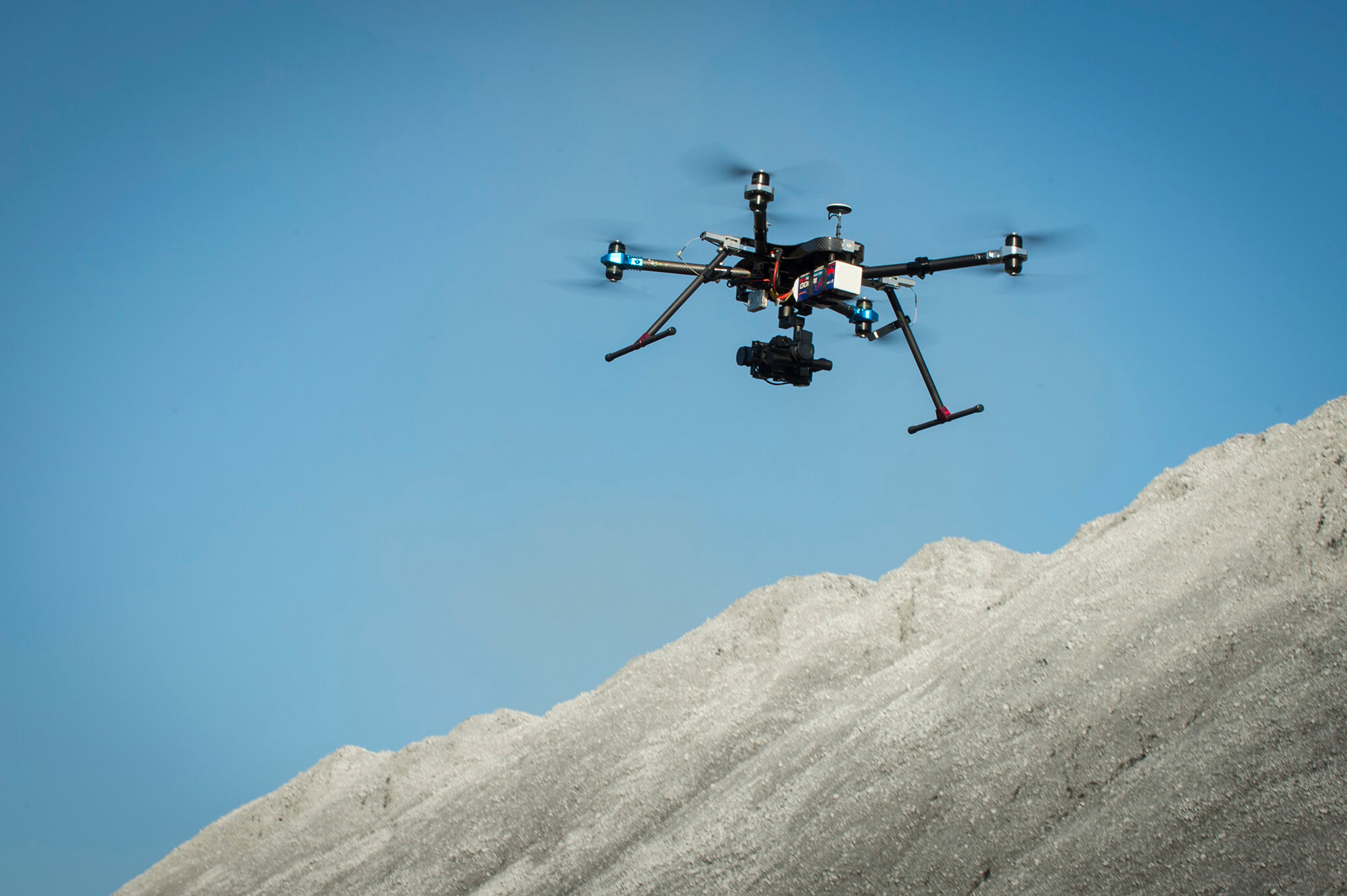
Onze milieuzorg
Onze milieuzorg
“We blijven op alle niveaus van de organisatie verbeteren op het vlak van milieuzorg.”
We beschikken sinds 2001 over een milieumanagementsysteem dat voldoet aan de eisen van de internationale norm ISO 14001. Het milieumanagementsysteem verplicht ons om onze milieuzorg op een gestructureerde manier aan te pakken, te beginnen met de identificatie van de belangrijke milieuaspecten waaraan we aandacht moeten schenken. Het milieuzorgsysteem wordt elk jaar geauditeerd door een externe onafhankelijke organisatie, die vaststelt of we aan alle normeisen blijven voldoen en of we blijven verbeteren op het vlak van milieubeheer. Het ISO 14001-certificaat biedt de garantie aan alle externe belanghebbenden, zoals buurtbewoners, omliggende bedrijven, overheden, leveranciers en klanten, dat ‘duurzaam ondernemen’ voor ons geen holle woorden zijn.
Eerste gemeenschappelijk ISO 14001-certificaat voor de cluster ArcelorMittal Belgium
11/‘18
opvolgingsaudit ISO 14001 bij ArcelorMittal Gent
12/‘18
certificatie-audit ISO 14001 bij ArcelorMittal Luik
01/‘19
ISO 14001-certificaat aan de volledige cluster ArcelorMittal Belgium toegekend.
18 maart 2019
Amines splitsen CO & CO2 voor verdere verwerking
ArcelorMittal Gent en Dow (Terneuzen) kondigden op 18 maart 2019 aan, samen te werken met verschillende partners aan een innovatieve technologie om CO en CO2 uit de procesgassen van de staalindustrie via chemische weg (met amines) te valoriseren. Dit project heet “Carbon2Value”.
De pilootinstallatie werd in 2018 op onze Gentse site geleverd. Na keuring en een uitvoerige testfase, kon in het voorjaar van 2019 het proevenprogramma beginnen. De officiële inhuldiging van de pilootinstallatie vond plaats op 18 maart 2019 in aanwezigheid van Philippe Muyters, Vlaams Minister van Werk, Economie, Innovatie en Sport.
“Ons Carbon2Value-project is een mooi voorbeeld van grensoverschrijdende industriële symbiose tussen de staalindustrie en de chemische industrie om de CO2-uitstoot terug te dringen.”
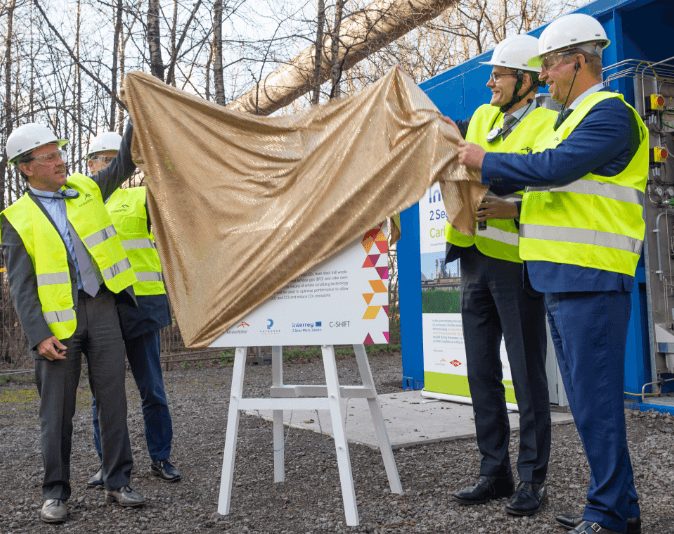
2 Mei 2019
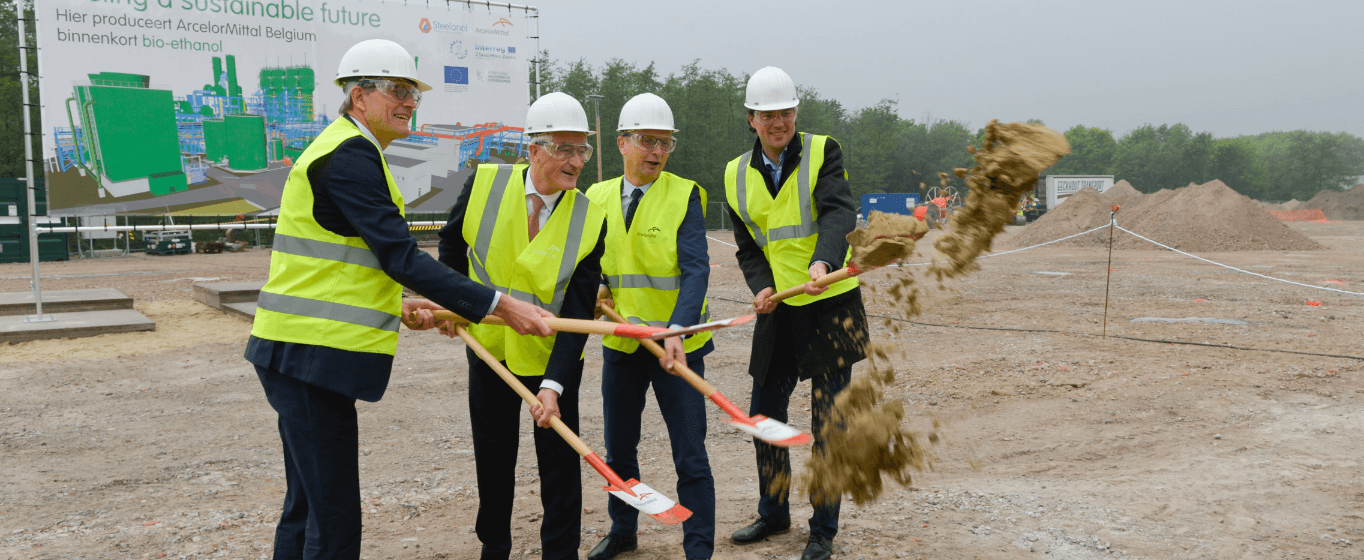
Op donderdag 2 mei 2019 werd, in aanwezigheid van Vlaams Minister-President Geert Bourgeois, de eerste spadesteek gegeven voor de bouw van twee nieuwe baanbrekende installaties om de koolstofuitstoot van ArcelorMittal Gent verder terug te dringen.
Hoogovengas wordt Bio-Ethanol
Een deel van de CO die we afscheiden via onze Carbon2Value-pilootinstallatie zullen we via de Steelanol-installatie tot bio-ethanol kunnen omvormen, om vervolgens te gebruiken als brandstof voor transport of voor de productie van kunststoffen.
“Onze Steelanol-installatie wordt de eerste industriële installatie in zijn soort in Europa, goed voor een jaarlijkse productie van 80 miljoen liter bio-ethanol.”
Deze technologie, onder licentie van het Amerikaanse LanzaTech waar we een partnerschap mee zijn aangegaan, maakt gebruik van microben die zich voeden met koolstofmonoxide om bio-ethanol te produceren. De indienstname en eerste productie van de Steelanol-installatie wordt tegen 2020 verwacht.
Verwerking houtafval tot biokoolstof
De Torero-installatie zal houtafval verwerken tot biokoolstof die geschikt is voor het hoogovenproces. Hierdoor kunnen we de injectie van fossiele poederkool in onze hoogovens verminderen, waardoor de CO2-uitstoot daalt. Dit biedt eveneens een alternatief voor het huidige verbranden van deze bijzonder moeilijke houtafvalstroom.
“De Torero-installatie zal in de beginfase jaarlijks 120.000 ton afvalhout omzetten in ongeveer 50.000 ton biokolen.”
De technologie van het torrefactieproces is ontwikkeld door het bedrijf Torr-Coal, het afvalhout zal geleverd worden door Renewi. De indienstneming en eerste productie worden verwacht tegen eind 2020.